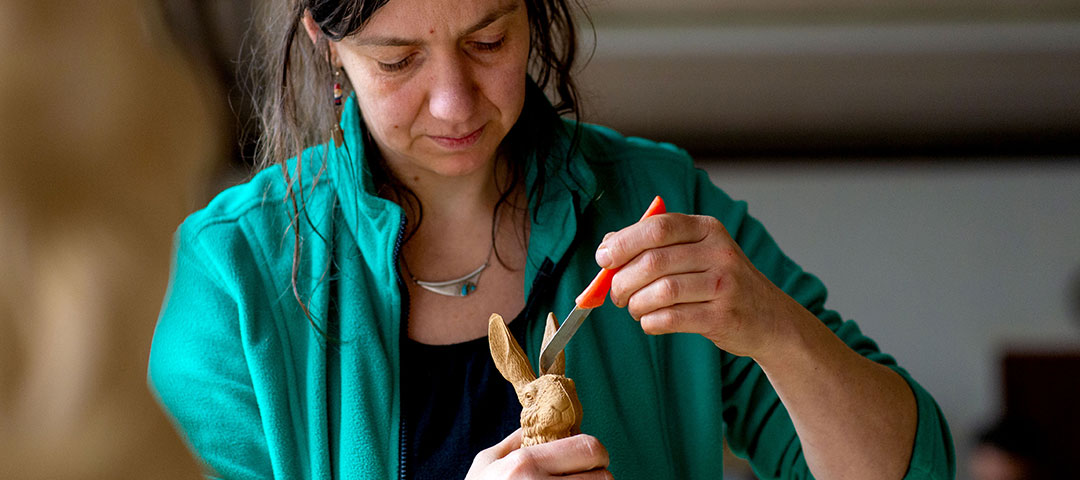
MANUFACTORY
The heart of our “glass” manufactory are the molds created in our traditional workshop throughout almost 150 years. Having been collected over four generations, the “Griebel” gnomes and ceramic animals are still being handcrafted in their historical form today – from the mixing of the clay to the finished figure.

As the only remaining traditional gnome factory in the world, we not only have molds that originate from our own workshop. Philipp Griebel and subsequently his descendants rescued numerous molds and models from the bankruptcy estate of other manufactories, which are now to be included in our range. Even though there are similarities between the figures due to the common master Dornheim and it is sometimes tricky to assign a gnome to its manufacturer or modeller, we consider it to be our responsibility to sift through this historical mold stock, catalogue it, and preserve it for posterity.
All our molds are unique forms that serve as master forms for both single-piece and serial production. Whether old or new, they embody the philosophy of Art Nouveau: attention to detail and proximity to nature. Their distinctive facial expressions and natural posture are characteristic of them, in spite of the challenge of creating a compact silhouette for the casting process.
The Production
The basis of our handicraft is clay, weathered feldspar, which is composed of remnants of quartz, mica, minerals, and organic substances. The very special mixture of our high-quality clay remains a secret.
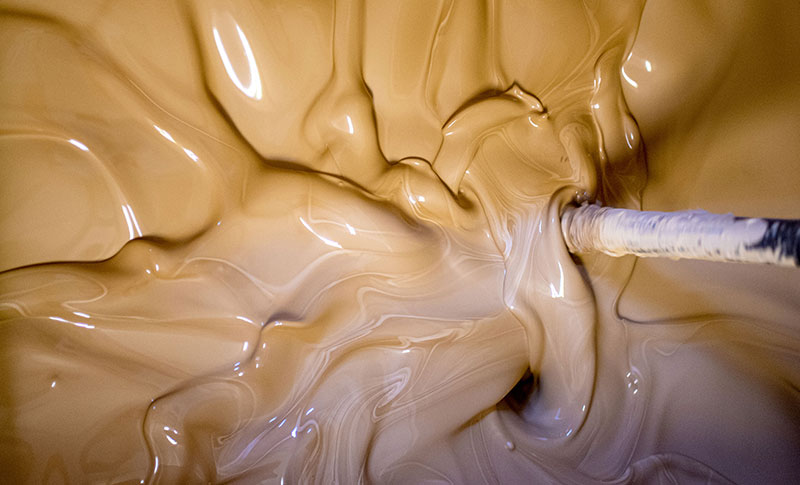
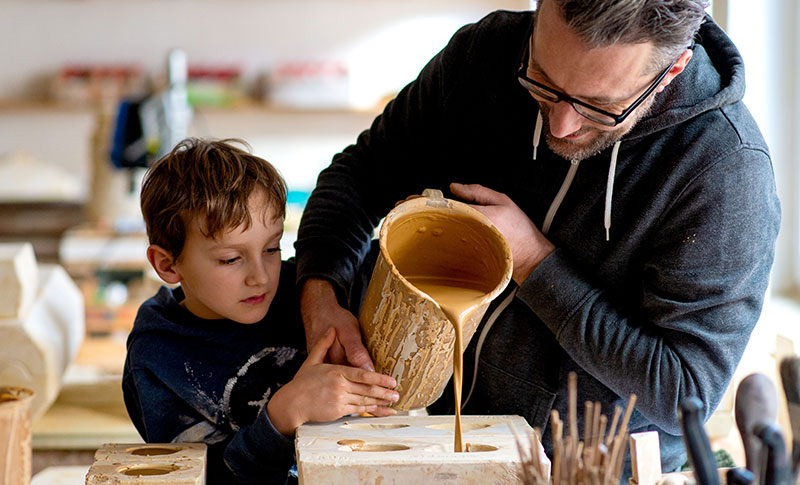
The basis of our handicraft is clay, weathered feldspar, which is composed of remnants of quartz, mica, minerals, and organic substances. The very special mixture of our high-quality clay remains a secret.
Watered and kneaded to a malleable, dough-like mass, it is poured free of impurities and air bubbles into our plaster models. There, it solidifies from the outside to the inside, and the remaining sludge is poured out after the desired wall thickness of the figure has been achieved (Hollow casting process).
This is where the work of our modellers starts, who remove casting seams with a knife or folding stick and smooth them out with a wet brush or sponge. The larger the mold, the more complex it becomes, with individual parts that are manually glued to the body for a perfect fit.
Patience is an important part of the craft as well, because after an adequate drying period, the mold first disappears into the furnace, where it is fired at not less than 1000 degrees in order to become a stable, waterproof, and almost frost-proof figure. Afterwards, it slowly cools down and only returns to the workshop light once it is completely cold again.
In the hands of the painters with their skilful and precise brushwork, it is then given its final appearance using water-soluble, fast-drying paints that are harmless to health. The face of a garden gnome alone requires ten layers of paint before a matte or glossy varnish completes the work, so the gnome can defy wind and weather in your garden.